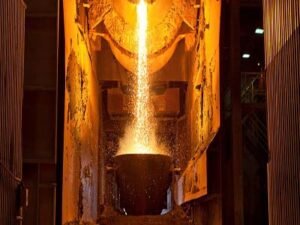
In the non-ferrous metal smelting industry, the selection of the right kiln needs to consider a number of factors.
1.Choosing according to the type of metal
– Copper smelting
– Flash furnace: If you are dealing with fine ground copper concentrate, flash furnace is a good choice. It can make the fine ore powder be heated and oxidized in an instant, with high production efficiency and low energy consumption, and the output of high concentration of sulfur dioxide flue gas is convenient for acid production, which is conducive to environmental protection and comprehensive utilization of resources.
– Reverberation furnace: For copper raw materials with complex composition and uneven particle size, reverberation furnace is more suitable. It has strong adaptability to raw materials and can be large-scale continuous production, but the thermal efficiency is low and the environmental protection pressure is greater.
– Lead and zinc smelting
– Blast furnace: widely used in heavy metal smelting such as lead and zinc. When dealing with complex ores containing multiple metal components, and the need to recover multiple valuable metals at the same time, the blast furnace has obvious advantages because it can effectively reduce the metal in a strong reducing atmosphere. However, it has high energy consumption and difficulty in flue gas treatment.
– Rotary kilns: If processes such as zinc roasting or clinker sintering are involved in alumina production, rotary kilns are the ideal choice. It can handle materials of different shapes and properties, and the production process is stable and continuous, but the thermal efficiency is not high, requiring fine operation management.
2. Considering the scale of production
– When large-scale production of non-ferrous metals, flash furnace and large reverberatory furnace, rotary kiln is a more suitable choice. Flash furnace melting strength is high, large reflector furnace and rotary kiln can continuously and stably process a large number of raw materials, which can effectively improve production efficiency.
– For small and medium scale production, blast furnaces or small rotary kilns can meet the demand. Although the equipment of blast furnace is relatively complex, it has good adaptability to raw materials; Small rotary kilns perform better in terms of flexibility and can adapt to different properties of materials.
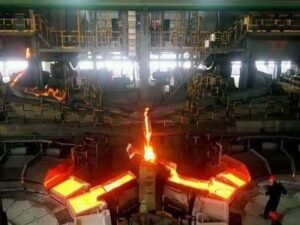
3.Energy utilization and cost
– Energy type and efficiency
If the local power resources are abundant and the price is reasonable, electric furnaces (such as electric arc furnaces, induction furnaces) are a good choice, especially in the production of some special steel and high-quality steel, which can accurately control the composition and quality, and have less impact on the environment.
– Fuel based: When fuel is the main energy source, the thermal efficiency of the kiln needs to be considered. The thermal efficiency of flash furnace and rotary kiln is relatively high after optimization, while the thermal efficiency of reverberation furnace is low, so the selection should be combined with the fuel cost.