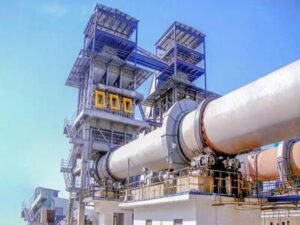
1.Drop brick red kiln
– Cause: poor quality of kiln lining and its inlay, or too thin after corrosion and not replaced on time.
– Solution: Choose high-quality refractory bricks, stop kiln to replace new bricks, improve the quality of inlaying, and prohibit pressure repair; Strengthen the batching work and improve the level of calcining operation.
2.Vibration of kiln cylinder
– Cause: the cylinder is not heated evenly, the bending deformation is too large, and the supporting wheel is empty; The meshing clearance of the gears is too large or too small; The interface bolt of the big gear ring is loose or broken; Transmission pinion wear seriously, resulting in steps; Foundation anchor bolts are loose.
– Solution: adjust the support wheel correctly; Adjust the meshing clearance of the size gear; Tighten or replace the big gear ring interface bolt; Change the transmission pinion; Tighten the anchor bolts.
3.Wheel liner overheats
– Reason: kiln center line is not straight, lining force is too large; The support wheel is incorrect and skewed, and the bearing thrust is too large; Bearing cooling water leakage, improper oil or lubrication deterioration, and oil mixed with other debris.
– Solution: correct the center line and adjust the load of the support wheel; Adjust the position of the support wheel; Timely oil change, repair water pipes, clean lining.
4.Wheel belt and support wheel failure
– Cause: the wheel belt and the backing plate are seriously worn, the gap is too large, and the radial deformation of the kiln barrel is increased; The center line of the support wheel is too skewed, the contact is uneven, and the local unit pressure increases. The gap between the wheel belt and the plate is too small or too large, the temperature is too high, there is dust and other debris; The axial thrust of the support wheel is too large, causing the friction and extrusion pressure between the wheel belt and the side stop ring to be too large.
– Solution: strictly control the gap between the wheel belt and the pad near the burning belt, and timely replace the pad or adjust the pad; Adjust the support wheel to reduce the skew degree; Adjust the gap and clean up the debris; Adjust the wheel to reduce thrust.
5.The preheater crust is blocked
– Cause: harmful elements in the raw materials exceed the standard and the ingredients are inappropriate; Kiln tail seal leakage; Improper operation results in cyclic enrichment of harmful components such as alkali, chlorine and sulfur.
– Solution: optimize the dosing scheme, control the operation, avoid reducing atmosphere; Manually clean the crust regularly to avoid incomplete combustion in the kiln; Dispose of the kiln tail sealing device when the kiln is stopped for maintenance.
6.The kiln skin is unstable and repeatedly falls off
– Reason: the raw material composition of the pre-homogenization facility fluctuates greatly, resulting in the fluctuation of the thermal system in the kiln.
– Solution: Do not take the remaining part of the material at the end of the pre-homogenized storage yard, keep the material level of the raw material warehouse above 50%, and appropriately reduce the feeding amount when detecting thermal fluctuations to stabilize the thermal system.
