In the cement industry, kiln is the core production equipment, its types are diverse, each kiln has its own characteristics and scope of application, together to promote the efficient cement production.
1. Rotary kiln
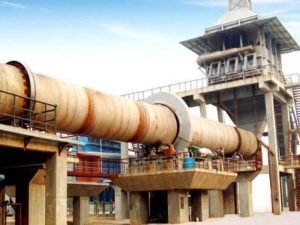
Rotary kiln is one of the most widely used kiln in cement industry. It has a cylindrical shape, is mounted at an angle and turns slowly. Raw material enters from the kiln tail, and gradually moves to the kiln head with the rotation of the kiln body. In this process, it successively experiences a series of complex physical and chemical changes such as drying, preheating, decomposition and firing. The advantages of the rotary kiln are significant, and its adaptability to raw materials is extremely strong, whether it is conventional raw materials such as limestone, clay, or alternative raw materials such as some industrial waste, it can be effectively treated in the rotary kiln. It can achieve large-scale, continuous production, high production efficiency, can meet the needs of modern cement industry mass production. However, the rotary kiln also has some shortcomings, such as its relatively low thermal efficiency, the need to consume a lot of fuel during operation, and because of the long kiln body and complex structure, the investment cost and maintenance cost of the equipment are relatively high.
2. Shaft kiln
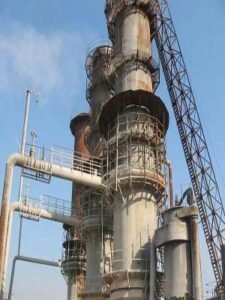
Shaft kilns also played an important role in the history of cement production. It is a kiln that is placed vertically, the material is added from the top of the kiln and calcined from top to bottom in the kiln. The advantage of shaft kiln is that its structure is relatively simple, the footprint is small, the equipment investment cost is low, suitable for some small cement enterprises or production applications under specific resource conditions and market demand. However, there are some insurmountable problems in the production process of shaft kiln, such as uneven calcination, which easily leads to unstable quality of cement clinker; At the same time, its environmental performance is poor, and the waste gas generated in the calcination process is difficult to be centrally treated, causing greater pollution to the environment. With the continuous progress of cement industry technology and the increasing requirements of environmental protection, the application of shaft kiln in modern cement production is gradually decreasing.
3. New dry cement kiln
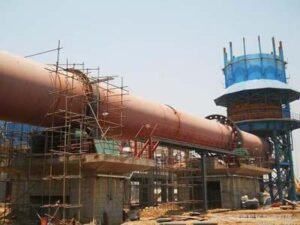
The new dry cement kiln is an advanced representative of modern cement industry. It takes suspension preheating and predecomposition technology as the core, the raw powder is suspended in the hot gas flow for preheating and predecomposition, and then enters the rotary kiln for clinker firing. The thermal efficiency of this kiln is greatly improved, which can save more than 30% of energy compared with traditional rotary kilns. At the same time, the production process of the new dry cement kiln has a high degree of automation, which can precisely control the raw material batching, calcination temperature, time and other parameters, so as to ensure the stable and excellent quality of cement clinker. In terms of environmental protection, it is equipped with advanced waste gas treatment system, which can effectively reduce the emissions of dust, sulfur dioxide, nitrogen oxides and other pollutants, in line with the requirements of modern society for the green production of cement industry. However, the construction cost of the new dry process cement kiln is higher, and the technical and management level also has higher requirements, which requires the enterprise to have a strong comprehensive strength to operate. These kilns commonly used in the cement industry play their respective roles in different historical periods, technical backgrounds and market demand, with the continuous innovation of science and technology and the deepening of the concept of sustainable development, cement kiln technology is also continuing to develop and improve, to achieve higher production efficiency, better product quality and better environmental performance.