In the glass industry, the kiln is the key equipment for glass production, its variety, different types of kiln for different glass production process and scale, the following are several commonly used kiln:
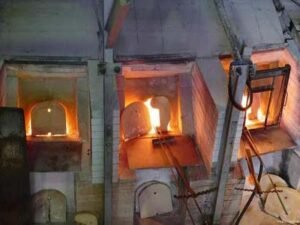
1. Glass melting kiln
Glass melting kiln is the core kiln of glass production, which can be divided into pool kiln and crucible kiln. Pool kiln is the most common large glass melting kiln, which has a large melting pool, glass raw materials in the pool after high temperature melting, clarification, homogenization to form glass liquid. Chi kiln has a large production capacity, suitable for large-scale continuous production of flat glass, bottle glass and other glass products. It can achieve efficient heat utilization, through reasonable combustion system and kiln body structure design, so that the fuel is fully burned, the heat is evenly transferred to the glass raw material. However, the construction cost of pool kilns is high, and once built, its production process is relatively fixed and less flexible. Crucible kiln is a small glass melting kiln, usually composed of multiple crucible, glass raw materials in the crucible melting. Crucible kiln is suitable for the production of special glass, art glass and other small batch, variety of glass products, its flexibility is strong, can be adjusted according to different glass formulations and production requirements, but the production efficiency is relatively low, high energy consumption.
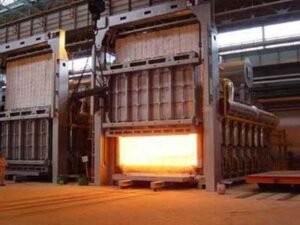
2. Annealing kiln
The annealing kiln plays a vital role in the glass production process. After the glass products are formed, there is a large internal stress, if not annealed, the glass is prone to crack and other quality problems. By precisely controlling the temperature and cooling rate, the annealing kiln gradually removes stress from the glass products during the annealing process. The working principle is to slowly cool the glass products from a high temperature state and anneal them according to a certain temperature system. There are many types of annealing kiln, such as intermittent annealing kiln and continuous annealing kiln. Continuous annealing kiln has high production efficiency, can meet the needs of large-scale glass production, can realize automatic control, and ensure the stability of annealing quality. Intermittent annealing kiln is suitable for small batch, special specifications of glass products annealing treatment, its flexibility is better, but the production efficiency is low.
3. Flower kiln
The kiln is mainly used for decorative processing of glass products, such as baking patterns and characters on the glass surface. Through heating, the glaze on the surface of the glass melts and adheres to the glass to form an exquisite decorative effect. It is characterized by precise temperature control requirements, generally using electric heating or gas heating. The electric flower kiln has the advantages of uniform heating and high temperature control precision, which can meet the requirements of high-quality flower baking technology, but the operation cost is high. Gas kiln has the advantages of fast heating speed and relatively low cost, but the temperature uniformity is slightly worse than that of electric kiln. The structural design of the kiln pays attention to the uniformity and stability of the internal temperature field to ensure that the decorative effect of glass products is consistent in the process of roasting flowers and improve the added value of products. These kilns commonly used in the glass industry play a unique role in different aspects of glass production, and their continuous development and innovation promote the continuous progress of the glass industry in terms of product quality, production efficiency and decoration technology.